Alumni Retool Studios to Produce Personal Protective Equipment
POSTED ON: April 15, 2020
As critical supplies stretch thin across New York area hospitals hit hard by the influx of COVID-19 patients, a number of Cooper alumni-led businesses are organizing creative efforts to support healthcare workers on the frontlines. The call for donations of Personal Protective Equipment (PPE) in particular has inspired alumni who work in 3D-printing, design, and fabrication to shift their operations to creating masks and other medical supplies while non-essential businesses in the State of New York remain closed.
“As makers and artists, we were able to gather resources and mobilize quickly,” says Lena Imamura A’08, co-founder of New York City-based contemporary neon studio Name-Glo. In early March, at the outset of the city’s coronavirus outbreak, Imamura and fellow co-founder Sas Simon were approached by a friend who works as a doctor at a major hospital about the possibility of 3D-printing PPE designs. They started printing protective face shields in coordination with the doctor and in turn, Imamura says, learned how to implement safety precautions, navigate the hospital bureaucracy, and respond to some of the supply chain breakdowns taking place. As similar calls for help came in from the broader medical community, the Name-Glo team went to work retooling their shop to scale their PPE production.
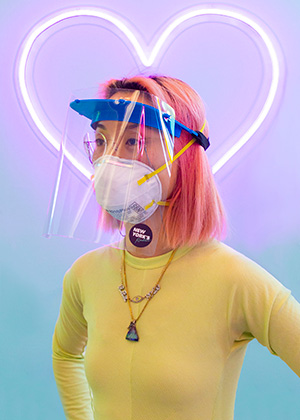
Using a design approved by the National Institute of Health, they began 3D-printing visors and assembling them into face shields with common materials such as foam, glue, plastic, and transparent acetate, mylar, or polycarbonate sheets. “The idea of making something like this was not at all foreign to us because we’re used to working with our hands and being resourceful,” Imamura says. “Our experience handling art and fragile neon contributed to our ability to handle the PPE safely and with care. We were lucky to be well-equipped.”
Name-Glo’s efforts have benefited from a collaborative network of artists, members of the DIY maker community, and other Cooper alumni, including Yuri Masnyj A’98, Imamura’s partner and an adjunct professor in the School of Art, and Taylor Shields A’09, a 3D-printing engineer at NYU’s LaGuardia Studio. The team has also been sharing their experience and resources with colleagues who are themselves using available materials to fabricate PPE. Hannah Rawe A’07, a former classmate of Imamura, has been communicating with the Name-Glo team while fabricating acrylic intubation boxes, which provide a protective barrier through which medical workers can access patients’ airways.
“One thing Yuri and I have been saying is that as School of Art alumni we’ve been training for this moment for a long time,” Imamura says. “As a philosophy, as a methodology, as a culture, the Cooper ethos has allowed us to have the resources, skills, and heart to do something like this. It’s also given us the confidence to see it through.”
Support has come from former classmates outside of the School of Art as well. “I always worked with an engineer during my time at Cooper,” Imamura explains. George Ketigian IE’07, director of prototype engineering at Silicon Valley investment firm Playground, has been working in tandem with Name-Glo to print and ship face shields. “George and I have remained in contact and although he’s on the West Coast, having an engineer get involved has been very helpful and informative,” says Imamura.
Drawing technical expertise from across disciplines has proven similarly valuable for SITU, another alumni-led business leading the charge to support healthcare workers. “What became clear pretty quickly is that working at the intersection of design, fabrication, and manufacturing has made us really well-equipped to respond to the current need for PPE,” says Brad Samuels AR’05, who leads the firm’s research division. “A lot of SITU’s designers are also fabricators and a lot of fabricators are designers.”
Founded by Samuels, Sigfus Breidfjord AR’05, Basar Girit AR’05, Aleksey Lukyanov-Cherny AR’05, and Wes Rozen AR’05, SITU is an architecture practice based in the Brooklyn Navy Yard. In addition to manually assembling face shields, the SITU team is working with healthcare providers to address the exposure risks of testing for COVID-19 on a large scale. Taking inspiration from the “phone booth” style of patient screening centers used in South Korea, they are developing a screening booth that can be rapidly deployed and attached to medical tents to provide contact-free outdoor coronavirus testing.
“There are emerging needs specific to this unprecedented situation that require new design solutions,” says Samuels. The team’s concept for testing patients while minimizing person-to-person contact first came about through conversations with an emergency coordinator at a local hospital. “As we spoke with medical professionals, a need was articulated to mitigate levels of exposure between doctors and patients and also exposure of patients to other patients,” he explains. “We wanted to take as little of their time as possible, so we interpreted that need as a design brief.”
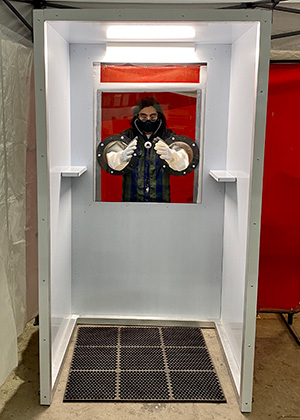
SITU’s prototype of the screening booth includes a transparent partition with sealed gloves embedded, allowing medical practitioners to examine patients without exposure and reducing the reliance on PPE. The booths are also easily sanitized between patient visits, making it possible for a large number of examinations to be conducted. SITU is now in the process of user-testing its prototype and hopes to soon refine its design and eventually coordinate with city agencies and hospitals to place testing booths in areas with high densities of coronavirus cases.
Several other Brooklyn Navy Yard tenants are already coordinating efforts with the City of New York. Among them is Crye Precision, a military clothing and equipment company founded by Cooper alumni Gregg Thompson ME’98; MME’01 and Caleb Crye A’97. With the help of women’s wear brand Lafayette 148, also based in the Navy Yard, Crye Precision is running a production line for surgical gowns to protect healthcare workers.
Mayor Bill de Blasio, who recently visited the Navy Yard, hopes their operation will be able to produce over 300,000 gowns by the end of April. “This production line is exactly the kind of solidarity that will get us through this,” he said. “Day by day, we are assessing what we need to keep our frontline workers safe — and the ability to produce protective equipment here in New York City is critical.”
Just outside of the city, in Westchester County, alumnus Greg Loibl ME’92 has similarly directed his company Poughkeepsie Revolutionary Cooling Systems, Inc. — producers of the Cooper Cooler, a rapid beverage cooler he invented as an undergraduate with former advisors Irv Brazinsky, Professor of Chemical Engineering, and George Sidebotham, Professor of Mechanical Engineering — to quickly shift operations to manufacturing PPE. Loibl is now producing 1,000 face shields per day and distributing them to Westchester healthcare workers.
Sourcing PPE has also taken forms other than directly producing them, including reaching out to neighborhoods and local communities. In Jackson Heights, Queens, Shekhar Krishnan BSE’06 helped organize the collection of 5,000 masks to be donated to the emergency and OBGYN departments at Elmhurst Hospital, which has been described as the epicenter of New York’s COVID-19 crisis. Krishnan is a lawyer and co-founder of Communities Resist Inc., an anti-displacement legal services and advocacy firm that defends low-income communities of color with a focus on tenants’ rights and housing justice. At the beginning of the month, Krishnan co-hosted a webinar on housing rights at a time when many face unemployment.
While some alumni are pivoting their operations or organizing mutual aid to meet the demand for medical supplies, others have been working in the PPE manufacturing space for years. Techmer PM, a materials design company founded by John Manuck CHE’69, who is the current chairman and CEO, announced this month a newly developed solution for enhancing fabrics used in the production of protective face masks. The company’s Charge Enhancer technology can be added to the production of particular types of filtration fabrics to enhance the material and help it retain an electrical charge that improves its filtration efficacy.
But as more and more people from outside the PPE industry look for ways to contribute their skills and resources to help with the coronavirus relief effort, concerns have been raised about distributing supplies where they’re most needed and protecting against liabilities. “It requires a level of trust in the people assembling these products and control over how many hands they’re going through,” says Imamura.
In the midst of an emergency, the alumni we spoke to say these concerns have not held them back from trying to help. As Samuels explains, relying on networks within the city to efficiently allocate resources and connecting people to operations that are best equipped to meet requests for PPE have been essential to responding quickly. Working with and listening to medical professionals has been equally important.
“This speed of innovation is uncomfortable for the field of medicine, but what that means is you need intensive and serious feedback from medical practitioners,” Samuels says. “What has been interesting is seeing how the need to get things out into the world quickly and to do it at a scale beyond the capacity of any one operation has engendered open-source collaborations that are so far outside the norm.”
See more alumni-led efforts at managing the COVID-19 crisis.